記者6月25日從國家電力投資集團有限公司科技成果發布會上海核工程研究設計院有限公司(以下簡稱“上海核工院”)專場了解到,在國和一號(CAP1400)開發過程中,已形成新產品、新材料、新工藝、新裝置等392項,形成知識產權4699項,形成行業、企業標準近200項。這組數字的背后,是中國核電行業數年的磨礪。
“這其中的很多材料和裝置原本都需要進口。通過重大專項的實施,這些產品和材料基本實現了國產化。對于我國可能出口核電的國家和地區,我們也相應申請了國外專利,確保將來走得出去。”國家科技重大專項“大型先進壓水堆核電站”總設計師、上海核工程研究設計院院長鄭明光在發布會上表示,國和一號/CAP1400的自主設計和開發帶動了國內制造業體系的躍升。
一個國家的核電實力強不強,首先要看有沒有自主設計能力。若不具備自主設計能力,只能是盤桓在中低端水平的翻版或觸及侵權紅線。核電站屬于安全標準極高、系統復雜且精密的超級工程,自主型號研制不可能是一路坦途。鄭明光此前接受專訪時曾回憶說,核電安全標準的大大提高,對整個設備的可靠性設計、系統的可靠性設計都是極大的考驗。再加上,彼時中國的裝備制造業尚難以滿足國和一號/CAP1400的要求,圍繞型號的創新目標,設計方與制造方需要“跳一跳才夠得著”。
回顧10年前,參照三代核電的設計規格書,國內沒有一家裝備企業能完整有效地制造出三代核電設備,通過引進三代核電AP1000自主化依托項目、國和一號/CAP1400重大專項及其他三代核電項目的拉動,國內培育出全產業鏈的三代核電設備供應能力,中國核電裝備實現了從二代到三代的重大跨越。反過來,得益于關鍵設備國產化、大容量和簡化系統、模塊化建造等特點,當前世界最大的非能動壓水堆核電站國和一號/CAP1400的經濟性格外突顯,肩負著中國核電技術出海、帶動中國核電裝備“走出去”的使命。
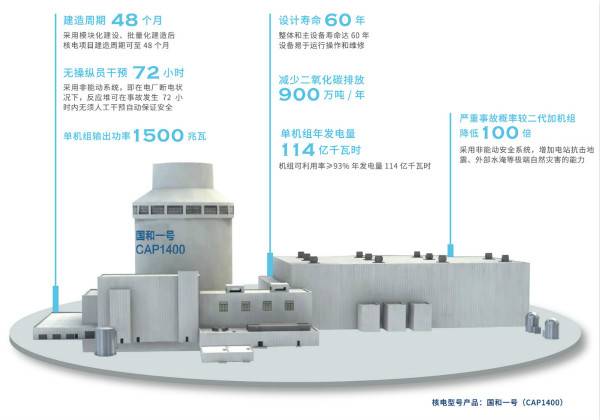
重大專項培育核電關鍵設備國產化
鄭明光在發布會上介紹稱,國和一號/CAP1400的開發屬于“高起點再創新”,它基于中國50年的核電廠研發、設計和工程經驗,基于中國44個機組20多年的安全建設和運行經驗,基于AP1000技術的消化吸收,也基于AP1000依托項目的建設經驗。
2006年11月,國家決定引進美國西屋公司AP1000技術。浙江三門核電站和山東海陽核電站共4臺機組被確定為中國三代核電自主化依托項目,2009年開始相繼開工,并于2018年底、2019年初相繼并網發電。
2008年2月15日,國務院常務會議正式通過壓水堆重大專項總體實施方案,并將CAP1400的研發和示范工程建設列為重大專項的重點任務,由AP1000的技術受讓方國家
核電技術公司牽頭,實行產學研結合,廣泛吸收有關單位共同攻關。
基于AP1000技術,CAP1400型號在確定之初就被定位為:安全性不低于AP1000、經濟性好于AP1000,整體設計壽命60年。其中,“C”為“中國”英文單詞的首字母,“A”、“P”分別代表“先進(Advanced)”和“非能動(Passive)”英文單詞的首字母,CAP1400的含義即為中國裝機容量為140萬千瓦的先進非能動核電技術,2018年這一型號的中文名被確定為“國和一號”。國和一號/CAP1400采用非能動安全系統,機組設計壽命60年,換料周期18個月,機組可利用率約93%,滿足目前世界上最嚴格的安全標準。
面對西屋公司提出的“135萬千瓦自主知識產權凈功率紅線”,中方設計團隊唯有對國和一號/CAP1400進行革命性的、更大幅度的創新。通過擴大安全殼直徑、增加蒸汽發生器流通面積等一系列根本性創新,國和一號/CAP1400的設計較AP1000開辟了另一片新天地:比如,采用反應堆系統性低壓損設計,流量增加了21%,揚程降低5%;堆芯方案從AP1000的157盒燃料組件變成了193盒燃料組件;蒸汽發生器提高傳熱效率,自主設計了汽水分離裝置和新型蒸汽限流器;反應堆壓力容器減少了焊縫;堆內構件取消了中子屏蔽板和流量分配裙,增加了吊籃剛度等等。

在頂層設計革新的基礎上,新的核電型號離不開新設備的支撐。三代核電更高的安全標準要求、技術標準要求、技術參數要求對國內設備廠商的軟硬件能力提出了新的挑戰,當時國產化設備的制造能力還未達到能制造如此大功率設備的水平。“2007年、2008年,當時我們以三代核電的設計規格書請制造企業生產設備,當時國內沒有一家企業能完整有效地制造出三代核電設備。”鄭明光回憶道。在此番時境下,一場設計方與設備方形成創新聯合體進行技術攻關的長跑隨之啟動。
在發布會上,上海核工院工程設備所副所長矯明分享了幾個三代核電關鍵設備和材料的國產化案例。核島關鍵設備價格往往高達幾千萬到數億元不等,重達幾百噸接近上千噸,對設計制造能力及制造商對于設計圖紙的理解能力的要求都非常高。
反應堆壓力容器是承載反應堆的核心設備、要求60年不可更換,設計壽命要求非常高。減少主環路的焊縫,可以大大提高核電技術安全性并減少運維時間,因此,國和一號/CAP1400創新性地采用了整體鍛造頂封頭管嘴和一體化底封頭。相比于堆焊,一體化焊件對制造廠裝備配套能力的要求又上了一個臺階。
功能類似于高壓鍋密封圈的反應堆壓力容器O型密封環,曾幾何時是國外采購經常被禁運的設備。“密封”是核電運行和事故狀態下防止泄漏的第一關,這種零部件對龐大的核電站來說看似微小,但曾是真正的“卡脖子”環節,O型密封環更是整個核電密封系統中最復雜、最重要的密封,從國外購買的價格高達幾百萬。該設備的國產化是國和一號/CAP1400研究開發過程中一個急需突破的難題。為此,上海核工院和和寧波天生密封件有限公司聯合成立了核電密封聯合研究中心,經過多年研制打破了國外壟斷,國產化后產品價格約為三四十萬元。
類似的由工程需求牽引出設備技術需求、設計方提出研制方案,設計方與制造方聯合攻克的關鍵設備和材料還包括大型鑄鍛件、蒸發器690合金傳熱管、焊接材料等等。為降低設備研制風險并培育良性的競爭氛圍,國和一號/CAP1400在開展設備研制及國產化過程中,對蒸汽發生器、壓力容器、主泵、主管道等關鍵設備均安排2-3家廠家進行培育,目前設備的國產化率已超過85%,可進一步達到90%以上。其余10%是可以國際采購的通用設備,目前沒有特別受制于人的物項。
在國和一號/CAP1400等三代核電技術的帶動下,國內各大制造企業完成了從不會到會、裝備制造能力從二代核電到三代核電的躍升,這同時支撐了如先進小堆等國內核電型號的開發。
當前,國內已具備年產10臺套以上的核電裝備制造能力,位居全球第一。一位國內一線裝備制造企業高管對澎湃新聞介紹,在這個過程中,中國企業的裝備能力在一些機械加工設備和重要工具工裝上已達到世界頂尖水平。中國裝備制造業的軟實力也得以提升,項目與技術管理也得以優化,人員隊伍的能力素養得到了進一步歷練。
做“減法”的簡化設計,經濟性富有競爭力
為保障核電機組的安全,國和一號/CAP1400在AP1000基礎上進一步提升了安全裕量:采用了非能動安全系統,利用物質的儲能、重力、對流、蒸發、冷凝等自然力,不依賴外部電源,能確保反應堆安全和余熱導出,事故后操縱員可不干預時間從“二代加”核電技術的30分鐘提高到72小時;堆芯損傷頻率和大量放射性物質釋放頻率較美國核電用戶要求文件限值低一個量級;具有系統性的嚴重事故預防和緩解措施;屏蔽廠房采用先進的鋼板混凝土結構,具備抗大型商用飛機惡意撞擊的能力等。
在此基礎上,國和一號/CAP1400還充分落實了福島事故后核安全的增強要求,包括提高縱深防御系統的抗震能力與電源可靠性,提高電廠抵御極端外部事件的能力,強化事故72小時后冷卻水和電力的供應能力,強化電廠應對超設計基準事故的能力等等。
在保證高安全性的前提下,現如今核電作為電力商品的屬性正在凸顯,作為“電”的經濟性,是決定核電在全球電力市場中競爭性的重要指標。據澎湃新聞了解,上海核工院曾經做過測算,國和一號/CAP1400批量化建造之后,倒推出的每千瓦時電價約為0.35至0.38元,頗具競爭力。
鄭明光對澎湃新聞表示,國和一號/CAP1400經濟性優于AP1000。一方面來源于機組效能、發電規模,另一方面是設備國產化之后具備更強的競爭力。因為設備的產業鏈是由多家制造企業構成,所以設備國產化、自主化后價格比引進設備便宜,同時促進了經濟性的提高,這主要是來自于系統性能的增強,系統效率的提高,經濟價格的合理。
最為核心的是,國和一號/CAP1400采用簡化設計和模塊化設計,用做“減法”的思路,把設備結構簡單化,采用“非能動”原理,緊急情況下不需要使用交流電源,僅僅依靠重力、熱循環和冷凝等自然手段作為動力排出余熱。與二代核電相比,國和一號/CAP1400的閥門數量減少了80.4%、泵的數量減少92.3%、管道數量減少58.5%、電纜數量減少了48.6%,在提高經濟性的同時,更便于運行和維護。同時,基于AP1000依托項目的經驗反饋,國和一號/CAP1400進一步優化了模塊化建造技術,批量化建造后核電項目的建造周期可至48個月,這大大少于目前國際主流核電機組工期。對于資金密集型核電產業而言,工期縮短的重要意義不言而喻。